LOTO Training - Ensuring Electrical Safety
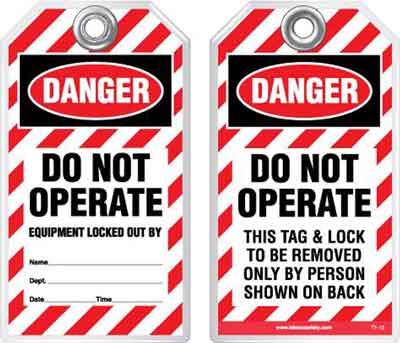
LOTO training is essential for protecting workers from the dangers posed by hazardous energy sources during the maintenance or servicing of machines or equipment. This process involves isolating and controlling energy sources to prevent the unintended release of energy that could result in injuries, equipment damage, or even fatalities. LOTO is regulated by the Occupational Safety and Health Administration (OSHA) under 29 CFR 1910.147, commonly known as the Control of Hazardous Energy standard. For electrical workers and other personnel involved in such tasks, understanding and following proper LOTO procedures is critical for maintaining a safe work environment.
Visit our LOTO Training Course Page
What is LOTO training, and why is it important for workplace safety?
It is a structured program designed to teach employees how to control hazardous energy and follow tagout procedures that prevent equipment from being inadvertently activated during maintenance or repair work. The instruction ensures that employees have the necessary knowledge and skills to identify energy sources and apply lockout devices or warning tags. These procedures are essential in industries with a high risk of exposure to hazardous energy, such as electrical, mechanical, pneumatic, and hydraulic systems. By undergoing this instruction, workers can minimize the risk of accidents and ensure compliance with OSHA regulations.
Who is required to undergo LOTO training, and what are their responsibilities?
It is required for three categories of workers: authorized employees, affected employees, and other employees. Authorized employees are responsible for implementing the lockout/tagout procedures. They have received specialized instruction that qualifies them to isolate and secure energy sources, ensuring that machinery cannot be re-energized during servicing. Affected employees are those who operate or work near the machines or equipment being serviced, but do not directly implement LOTO procedures. They must be aware of the importance of LOTO protocols to avoid accidental reactivation of equipment. Other employees, who may be in the vicinity but not directly involved, also need to understand the potentially hazardous nature of the work and keep a safe distance.
What are the key steps involved in a proper LOTO procedure?
A proper LOTO procedure follows a series of steps to ensure the safety of workers. These steps include identifying and isolating the hazardous energy sources, de-energizing the equipment, and applying lockout devices or tags. After securing the energy sources, the worker must verify that the machine is fully isolated and cannot be reactivated before maintenance begins. Tagout procedures are critical in this process, as they involve placing warning labels on energy isolation points, ensuring everyone in the area understands the equipment is not to be energized. Once maintenance is complete, the lockout devices are removed only after ensuring that all workers are safely out of harm's way.
How often should LOTO training be conducted, and what are the regulatory requirements?
OSHA mandates that this instruction be conducted whenever a new employee is hired, when job assignments change, or when new machines or equipment are introduced into the workplace. Additionally, if there is any reason to believe that employees' knowledge and skills in controlling hazardous energy need improvement, retraining must be provided. While OSHA requires new instruction upon these changes, companies are encouraged to provide regular refresher courses to ensure employees remain knowledgeable and competent in controlling hazardous energy sources.
What are the most common mistakes made during LOTO procedures, and how can they be avoided?
Some common mistakes during LOTO procedures include failure to fully isolate all hazardous energy sources, improper application of lockout devices, and neglecting to verify that the equipment is fully de-energized before maintenance begins. Another mistake is inadequate communication between workers, which can lead to accidental re-energizing of machinery. To avoid these errors, companies should ensure that workers have thorough knowledge and skills of the procedure, follow OSHA standards, and maintain consistent communication among team members. Regular refresher courses also help reinforce best practices and prevent lapses in safety.
This kind of electrical safety instruction is essential for ensuring the safety of workers who come into contact with hazardous energy sources. By following the 29 CFR 1910.147 standard, companies can protect their employees, reduce workplace accidents, and comply with OSHA regulations. Through proper tagout procedures and ongoing instruction, workers will be equipped with the knowledge and skills needed to control hazardous energy effectively, ensuring a safer and more compliant workplace.
On-Site Training
Interested in cost effective, professional on-site electrical training?
We can present an Electrical Training Course to your electrical engineering and maintenance staff, on your premises, tailored to your specific equipment and requirements. Click on the link below to request a Free quotation.
EF PARTNER MEDIA
Product Showcases
Shared Media