Battery advances led the charge for Volt
I thought it was the work of a designer gone crazy.
It turns out the armrest was actually the front end of the 450-pound, state-of-the-art lithium-ion battery that powers the new Volt.
For all these hybrid plug-in electric vehicles, the key — and the challenge — is the battery.
Chevy claims its Volt, due in showrooms by May 2010, will get 230 miles per gallon. And that's city driving. My turn in the Volt's driver's seat did not include a test drive, but it was a start to understanding a vehicle slated to sell for $40,000. Federal tax credits might knock another $7,500 off your cost.
The prototype Volt's battery bisects the car, running from the rear axle to the engine in front. The designers did what they could to camouflage it, but someone like me accustomed to riding in full-sized sedans will notice immediately that the battery takes up a big chunk of butt and elbow room.
The hard-to-miss battery is the most visible evidence of the big challenge in making electric hybrids. Figuring out how to make a battery that is small, light, energy dense, nearly infinitely rechargeable and cheap is no drive in the park.
Batteries have been the Achilles heel of electric-powered cars since the turn of the century. Electric cars peaked shortly after 1908, when Henry Ford started making his Model T, which used a gas-powered internal-combustion engine. The gas-powered cars proved to be far cheaper than the electric-powered cars.
In 75 years, batteries still aren't good enough to persuade many manufacturers or drivers to make the leap to battery power.
"If you look at the (battery) technology that's available now — lead acid, nickel-metal-hydride, lithium ion — none of them are sufficient to make a paradigm shift," said C. Spike Narayan, manager of science and technology at IBM's (IBM) Almaden Research Center in San Jose, Calif. IBM is using its expertise in supercomputing and nanotechnology to develop batteries.
"The technology needs to be five to 10 times better if you are going to change the way people look at electric vehicles," said Narayan, who heads up IBM's battery team.
General Motors executive Robert Kruse says that even as the company readies the Volt, it's working on replacement batteries.
"Normally, we develop Gen 1, launch it and learn from it, and then we develop Gen 2. It's very serial. What we're doing now — because batteries are so critical — we're working on Gen 2 and Gen 3 battery systems while we are launching the Gen 1 Volt. That is very unusual," said Kruse, executive director of GM's global vehicle engineering, hybrids, electric vehicles and batteries unit.
Many battery innovators say the next big thing in battery technology will be a variation on the lithium-ion battery, called lithium air. It uses the surrounding air as a cathode — the positively charged battery terminal — pairing it with a lithium anode. Narayan says lithium-air batteries can provide 10 times as much energy as a lithium-ion batteries, at about one-tenth the weight.
"If you look at the energy density you can get and how much energy you can store, lithium air is the best alternative," he said.
Unfortunately, even with big brains working on the problem, lithium-air batteries aren't ready for prime time. Nobody has figured out how to recharge one, and lithium-air batteries are very sensitive to water in the air, so rain could be major, major trouble.
PolyPlus Battery, a privately held company based in Berkeley, Calif., is on its way to solving these problems, says Steven Visco, chief technical officer of the 20-year-old, 27-employee firm. PolyPlus, which owns 72 patents on battery technology, has created a membrane that draws the oxygen through and keeps out the hydrogen. A lithium-air battery made with a PolyPlus design can even operate underwater.
"Our next step is to build a rechargeable battery," Visco said, "but that will take lots of R&D."
Narayan estimates a viable lithium-air battery is about five years away. Visco says that's optimistic. Both men point to the lack of an established U.S.-based battery manufacturing industry as one stumbling block. "The government will have to jump in," Narayan said.
It is. The Department of Energy's Argonne National Laboratory recently announced it's moving away from its 10-year-old commitment to developing lithium-ion battery technology to a new program focused on lithium-air batteries.
Jeff Chamberlain, who heads up business development in the office of technology transfer for Argonne, says the challenges to developing lithium-air batteries are great, but the results will be "game changing.... The payoff is enormous."
Lithium-air batteries will have the capacity to let cars travel hundreds, maybe thousands of miles, without a charge. Separately, they are also seen up ahead as a possible answer to a big problem — as a solution for storing solar and wind energy.
"If we are going to become energy independent, storage is the biggest issue," Chamberlain said. "Lithium-air batteries promise to be safer, with higher power and higher energy at less cost."
Asia dominates the battery industry, Chamberlain says, largely because it leads in electronics manufacturing. But he says that once the U.S. devises a battery like the lithium air that makes e-cars practical, battery manufacture will follow.
Some people argue that the U.S. is in danger of trading its dependence on foreign oil for dependence on lithium, foreign intellectual property and cheap labor.
Chamberlain disagrees. The largest battery makers are based in Japan, where the cost structure is similar to the U.S., he says. The big cost of entry to battery manufacture is the $300 million cost of building a battery plant. China recently has built 40 of them. But the U.S. can catch up, especially if it's able to develop a technology that recycles lithium, Chamberlain says.
"Once recycling kicks in, lithium is going to be a cheap commodity," he said.
In August, the U.S. Department of Energy awarded nearly $2.5 billion in grants to nearly 40 companies and universities to encourage domestic battery production. One recipient was lithium-ion car battery maker A123 Systems (AONE), which raised $378 million with a successful initial public offering just recently.
GM received $240 million for the Volt, while Volt battery maker LG Chem received $151 million.
The battery grants were "a bold move," said GM's Kruse, "but (we're just) playing catch-up with the commercialization of today's technology."
Related News
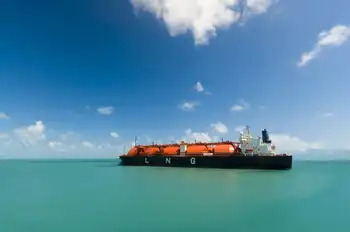
German official says nuclear would do little to solve gas issue
BERLIN - Germany’s vice-chancellor has defended the government’s commitment to ending the use of nuclear power at the end of this year, amid fears that Russia may halt natural gas supplies entirely.
Vice-Chancellor Robert Habeck, who is also the economy and climate minister and is responsible for energy, argued that keeping the few remaining reactors running would do little to address the problems caused by a possible natural gas shortfall.
“Nuclear power doesn’t help us there at all,” Habeck, said at a news conference in Vienna on Tuesday. “We have a heating problem or an industry problem, but not an electricity problem…