Construction of Transformer
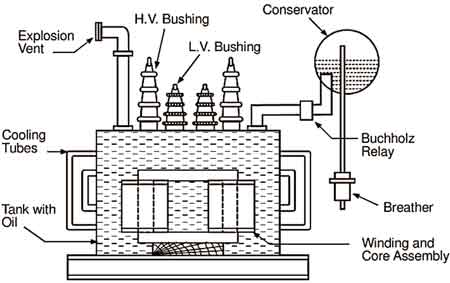
Construction of transformer involves core, windings, insulation, and cooling systems, converting voltage levels efficiently. Learn about laminated cores, primary and secondary windings, and design principles for power distribution and electrical energy conversion.
What is the Construction of a Transformer?
The construction of a transformer involves assembling its core, windings, insulation, and enclosure. It:
✅ Involves laminated iron core, primary and secondary windings, and insulation systems
✅ Ensures efficient voltage transformation and minimal energy loss
✅ Includes cooling, protective enclosures, and structural components for durability
Key Components and Functions
For a complete overview of large-scale utility applications, see our detailed guide on utility transformers.
Core
The core provides a path for magnetic flux and is typically constructed from high-permeability silicon steel to minimize losses. Laminating the core into thin sheets reduces eddy current loss and hysteresis loss, improving efficiency. The core type construction of a power transformer is designed to optimize efficiency by minimizing hysteresis and eddy current losses through the use of laminated, high-permeability steel. In contrast, a shell type transformer surrounds the windings with core material, improving magnetic coupling and reducing leakage flux. Each design has its advantages, with core type offering easier maintenance and shell type providing enhanced mechanical strength and fault tolerance in demanding applications.
Windings
The primary and secondary windings are made from insulated copper or aluminum conductors. Their arrangement and number of turns determine the voltage ratio. The primary winding receives input voltage, creating a magnetic field in the core, which induces voltage in the secondary winding for output.
Insulation
Insulating materials prevent electrical contact between windings and the core, ensuring safety and preventing short circuits. Depending on the transformer type, insulation may be paper-based, resin-coated, or oil-immersed.
Enclosure
The enclosure shields the internal components from dust, moisture, and mechanical damage. In outdoor or industrial settings, enclosures are designed to be weather-resistant and robust.
Learn how a 3-phase transformer design improves efficiency, load balancing, and power distribution in industrial systems.
Core Types and Materials
Transformers can be built using different core configurations:
-
Core-form: Windings surround the core limbs.
-
Shell-form: The core surrounds the windings for added mechanical strength.
-
Toroidal core: A compact, donut-shaped core offering reduced noise and higher efficiency.
Common materials include:
-
Grain-oriented silicon steel for high efficiency and low core loss.
-
Amorphous steel for very low no-load losses.
-
Ferrite cores for high-frequency applications.
Dive deeper into the essential transformer components that make up modern designs and ensure long-term reliability.
Winding Construction
Windings are layered and insulated to manage heat and prevent breakdown. Step-down transformers have more turns on the primary side, while step-up transformers have more turns on the secondary side. The winding layout also influences cooling efficiency and mechanical strength. Explore how distribution transformers deliver voltage at usable levels for residential, commercial, and light industrial loads.
Insulation and Cooling Systems
Dry-type insulation (epoxy, varnish) is used for indoor or low-maintenance applications.
Oil-impregnated paper insulation is common in high-voltage transformers, with mineral oil serving both as insulation and coolant. Cooling may be enhanced using:
-
Radiators and heat exchangers
-
Cooling fans for forced-air circulation
-
Oil pumps for forced-oil cooling in large power units
Drying processes remove moisture from insulation materials, increasing dielectric strength and service life. Learn how transformer insulation types and materials protect against faults, moisture, and electrical breakdown.
Bushings and Voltage Taps
Bushings provide insulated pathways for electrical conductors to pass through the transformer tank, maintaining safety and preventing leakage currents.
Tap changers allow operators to adjust voltage ratios to compensate for load variations, ensuring consistent performance and power quality. Discover why transformer oil is crucial for both cooling and insulation in high-voltage transformer systems.
Structural and Safety Features
Protective measures include:
-
Pressure relief devices to release excess internal pressure.
-
Buchholz relays in oil-filled transformers for early fault detection.
-
Temperature sensors to monitor winding and oil temperatures.
-
Seismic bracing in earthquake-prone regions.
These systems help maintain safe operation, extend lifespan, and prevent catastrophic failures.
The construction of a transformer blends precision engineering, advanced materials, and robust safety features. By selecting the right core type, winding configuration, insulation system, and cooling method, transformers can deliver efficient voltage transformation, low losses, and decades of reliable service in power systems worldwide.
Related Articles
On-Site Training
Interested in cost effective, professional on-site electrical training?
We can present an Electrical Training Course to your electrical engineering and maintenance staff, on your premises, tailored to your specific equipment and requirements. Click on the link below to request a Free quotation.
EF PARTNER MEDIA
Videos
Product Showcases
Shared Media