Electric Motor Design Engineering
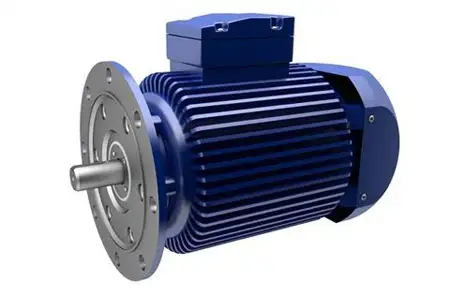
Electric motors, both AC motors and DC motors, come in many shapes and sizes. Some are standardized electric motors for general-purpose applications. Other electric motors are intended for specific tasks. In any case, electric motors should be selected to satisfy the dynamic requirements of the machines on which they are applied without exceeding rated electric motor temperature. Thus, the first and most important step in electric motor selection is determining load characteristics - torque and speed versus time. Electric motor selection is also based on mission goals, power available, and cost.
Starting and running torque are the first parameters to consider when sizing electric motors. Starting torque requirements for electric motors can vary from a small percentage of full load to a value several times full-load torque. Starting torque varies because of a change in load conditions or the mechanical nature of the machine, in which the electric motor is installed. The latter could be caused by the lubricant, wear of moving parts, or other factors. Electric motors feature torque supplied to the driven machine which must be more than that required from start to full speed. The greater the electric motor’s reserve torque, the more rapid the acceleration.
Electric motor drive systems that use gear reducers have parts that rotate at different speeds. To calculate acceleration torque required for these electric motors, rotating components must be reduced to a common base. The part inertias are usually converted to their equivalent value at the drive shaft.
ELECTRIC MOTORS - POWER RATING
Electric motors offer the horsepower required to drive a machine, which is typically referred to as electric motor load. The most common equation for power-based electric motors on torque and rotational speed is: hp = (torque X rpm)/5,250. If the electric motor’s load is not constant and follows a definite cycle, a horsepower versus time curve for the driven machine is helpful. From this curve, both peak and rms the electric motor’s horsepower can be determined. Rms load horsepower indicates the necessary continuous electric motor rating. Peak load horsepower is not necessarily an indication of the required electric motor rating. However, when a peak load is maintained for a period of time, electric motors feature a rating, which usually should not be less than peak load horsepower.
DUTY CYCLE - ELECTRIC MOTORS
Continuous steady-running loads over long periods are demonstrated by fans and blowers. On the other hand, electric motors installed in machines with flywheels may have wide variations in running loads. Often, electric motors use flywheels to supply the energy to do the work, and the electric motor does nothing but restore lost energy to the flywheel. Therefore, choosing the proper electric motor also depends on whether the load is steady, varies, follows a repetitive cycle of variation, or has pulsating torque or shocks. For example, electric motors that run continuously in fans and blowers for hours or days may be selected on the basis of continuous load. But electric motors located in devices like automatically controlled compressors and pumps start a number of times per hour. And, electric motors in some machine tools start and stop many times per minute.
Duty cycle is a fixed repetitive load pattern over a given period of time which is expressed as the ratio of on-time to cycle period. When operating cycle is such that electric motors operate at idle or a reduced load for more than 25% of the time, duty cycle becomes a factor in sizing electric motors. Also, energy required to start electric motors (that is, accelerating the inertia of the electric motor as well as the driven load) is much higher than for steady-state operation, so frequent starting could overheat the electric motor. For most electric motors (except squirrel-cage electric motors during acceleration and plugging), current is almost directly proportional to developed torque.
At constant speed, torque is proportional to horsepower. For accelerating loads and overloads on electric motors that have considerable droop, equivalent horsepower is used as the load factor. The next step in sizing the electric motor is to examine the electric motor’s performance curves to see if the electric motor has enough starting torque to overcome machine static friction, to accelerate the load to full running speed, and to handle maximum overload.
ELECTRIC MOTORS - SERVICE FACTORS
A change in NEMA standards for electric motor service factors and temperature rise has been brought about because of better insulation used on electric motors. For instance, a 1.15 service factor - once standard for all open electric motors - is no longer standard for electric motors above 200 hp. Increases in electric motor temperature are measured by the resistance method in the temperature rise table. Electric motors feature a nameplate temperature rise which is always expressed for the maximum allowable load.
That is, if the electric motor has a service factor greater than unity, the nameplate temperature rise is expressed for the overload. Two Class-B insulated electric motors having 1.15 and 1.25 service factors will, therefore, each be rated for a 90°C rise. But the second electric motor will have to be larger than the first in order to dissipate the additional heat it generates at 125% load. Electric motors feature a service factor, which indicates how much over the nameplate rating any given electric motor can be driven without overheating. NEMA Standard MGI-143 defines service factor of an ac motor as “...a multiplier which, when applied to the rated horsepower, indicates a permissible horsepower loading which may be carried under the conditions specified for the service factor...” In other words, multiplying the electric motor’s nameplate horsepower by the service factor tells how much electric motors can be overloaded without overheating.
Generally, electric motor service factors: * Handle a known overload, which is occasional. * Provide a factor of safety where the environment or service condition is not well defined, especially for general-purpose electric motors. * Obtain cooler-than-normal electric motor operation at rated load, thus lengthening insulation life.
From: Electric Motors and VFDs Handbook, Vol 3, The Electricity Forum
On-Site Training
Interested in cost effective, professional on-site electrical training?
We can present an Electrical Training Course to your electrical engineering and maintenance staff, on your premises, tailored to your specific equipment and requirements. Click on the link below to request a Free quotation.
EF PARTNER MEDIA
Product Showcases
Shared Media