What is Starting Current? Motor Efficiency Explained
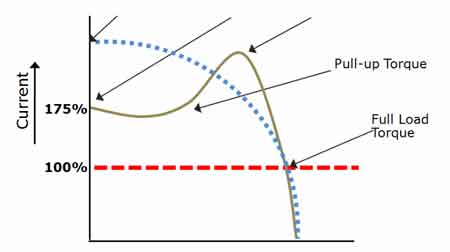
What is starting current? It's a question every industrial electrician needs to understand thoroughly to ensure the safety and efficiency of electrical systems. This surge of electricity, far exceeding normal operating current, occurs in the instant an electrical device is switched on. From preventing unexpected short circuit trips and equipment damage to implementing effective mitigation strategies like soft starters and star-delta configurations, this article provides a comprehensive overview of starting current, its causes, effects, and practical solutions. Read on to gain the knowledge necessary to confidently tackle starting current challenges in your industrial electrical work.
Starting current, commonly referred to as high resistance inrush current, is the initial surge of electrical energy required to power up a device such as an induction motor. This brief but intense burst occurs the moment the device is switched on and is often significantly higher than the operational current drawn during regular operation. This phenomenon is a critical consideration for engineers and electricians when designing systems that must accommodate the demands of motor starting, especially in industrial settings where electric motors play a pivotal role.
One of the key reasons starting current is higher than running current is the low initial impedance of devices like electric motors. At the moment of activation, motors face the challenge of overcoming inertia while simultaneously creating the magnetic fields necessary for operation. This lack of back electromotive force (EMF), which usually opposes and reduces the flow of energy during regular operation, means the motor draws a large amount of energy from the system. In devices such as power converters, the charging of internal capacitors can also contribute to this surge, amplifying the demand placed on the system.
The effects of this high initial demand on an electrical system can be significant. For instance, circuit breakers and fuses may trip under the sudden load, causing unnecessary interruptions in power supply. Voltage dips are another common consequence, especially when the motor starting process draws more energy than the system can momentarily provide. These dips can disrupt sensitive equipment connected to the same circuit, creating a cascading effect of performance issues. Over time, the repeated stress from this surge can degrade wiring insulation and other electrical components, reducing their lifespan and increasing maintenance costs.
Mitigation strategies are essential for managing starting current and ensuring system reliability. Soft starters are widely used to gradually increase the voltage applied to the motor, thereby controlling the intensity of the surge. This technique prevents abrupt spikes and reduces the stress on the system. Another effective method is the star-delta configuration, where the motor begins operation in a star connection to limit energy draw and then transitions to a delta connection for full load operation. Variable frequency drives (VFDs) are also an excellent solution, as they offer precise control over the voltage and frequency supplied to the motor during startup. Properly sizing circuit protection devices and incorporating inrush current limiters are additional steps that can be taken to minimize the impact.
Practical examples of starting current can be found in everyday and industrial applications alike. Electric motors in HVAC systems often exhibit this surge when compressors or large fans start up. In manufacturing, motor starting occurs in conveyors, pumps, and other heavy machinery, requiring systems designed to handle these bursts without compromising efficiency. Even household appliances such as refrigerators and air conditioners are subject to inrush current, albeit on a smaller scale.
Understanding starting current also requires distinguishing it from running current. While the former represents the initial, temporary surge of energy, the latter is the steady flow of electricity required to maintain operation. The difference is particularly pronounced in induction motors, where starting current can be up to six to eight times greater than the full load current. Calculating the expected starting current typically involves data provided by motor manufacturers or using specific formulas tailored to the device.
By implementing strategies to reduce starting current, the efficiency and longevity of electrical systems can be significantly improved. Soft starters, VFDs, and star-delta configurations are not only effective in mitigating the surge but also contribute to energy savings and system stability. Proper design and maintenance ensure that these strategies are optimized for the specific needs of each application, making starting current less of a burden and more of a manageable challenge.
In essence, starting current is the initial surge of electricity that flows through an electrical device when it's first turned on. This surge, often significantly higher than the device's normal operating current, occurs due to the low initial impedance of components like motor windings. While essential for getting devices running, high starting current can cause voltage dips, trip circuit breakers, and even damage equipment. Understanding this phenomenon and implementing mitigation strategies, such as soft starters and star-delta starting, are crucial for ensuring the safe and efficient operation of electrical systems.
On-Site Training
Interested in cost effective, professional on-site electrical training?
We can present an Electrical Training Course to your electrical engineering and maintenance staff, on your premises, tailored to your specific equipment and requirements. Click on the link below to request a Free quotation.
EF PARTNER MEDIA
Product Showcases
Shared Media