Mixing carbon into cement looks viable
If it works on a mass scale, the company, Calera, could turn that carbon into gold.
Cement production is a large source of carbon emissions in the United States, and coal-fired electricity plants are the biggest source. As nations around the world press companies to curb their greenhouse-gas emissions, a technology that makes it profitable to do so could be very popular. Indeed, CaleraÂ’s marketing materials may be one of the rare places where glowing quotes from a coal company and the Sierra Club appear together.
“With this technology, coal can be cleaner than solar and wind, because they can only be carbon-neutral,” said Vinod Khosla, the Silicon Valley billionaire. His venture capital firm, Khosla Ventures, has invested about $50 million in Calera. Calera has announced that Peabody Energy, the world’s biggest coal company, has invested $15 million.
Although Calera has a pilot project up and running, it is still not clear that the process can be used on a large scale or that anyone will buy the cement it makes.
Some climate scientists and cement experts are dubious that Calera can produce large quantities of cement that is durable and benign for the environment.
“People have been looking for ways to do this for 15 years,” said Ken Caldeira, an expert on the carbon cycle who is a senior scientist with the Carnegie Institution for Science at Stanford. “The idea that they’re going to come up with something that’s both economic and scalable? I’m highly skeptical.”
Major carbon emitters and green technology companies have been trying to figure out ways to capture and store carbon, such as injecting it into the ground, in case Congress begins to regulate carbon emissions.
Calera says that by turning carbon into a building material, it will make carbon reduction economically attractive even in places where there are no government subsidies or carbon taxes. “In this case, it’s actually a profit center,” said Brent Constantz, Calera’s founder and chief executive.
Mr. Constantz, who is a consulting professor at the Stanford School of Earth Sciences, has spent his career studying and creating different kinds of cement. As a graduate student, he studied how corals in the Caribbean use carbon dioxide to make their skeletons. He started two companies, Norian and Skeletal Kinetics, that make a calcium phosphate cement that surgeons use to repair broken bones.
In 2007, he and Mr. Khosla hatched plans for Calera. Today, Mr. Khosla is effectively part of the management team, involving himself in details and speaking with Calera executives daily.
While the company declines to share precise details of its process, it does say it combines carbon dioxide with seawater or groundwater brine, which contain calcium, magnesium and oxygen. It is left with calcium carbonate and magnesium carbonate, which are used in making cement and aggregate. It plans to sell it to concrete companies for use in pavement.
To make its cement more acceptable to manufacturers of traditional Portland cement, it is also making concrete blends of 20 percent Calera cement and 80 percent Portland cement, the calcium silicate binder used in concrete for buildings, highways and bridges.
In Moss Landing, on the shore of Monterey Bay, a huge natural gas power plant owned by Dynegy spews dirty gray smoke, called flue gas. It is full of carbon dioxide, a greenhouse gas.
Today, big, rusty pipes snake from the power plant to CaleraÂ’s demonstration cement plant. Calera pumps the flue gas into a big blue container, in which seawater from the nearby ocean is sprayed through the gas, producing a milky white liquid.
The liquid is then pumped into a giant strainer, which separates the solids from the water and spits out a white substance that looks like toothpaste. In a spray dryer, hot air — the waste heat from the flue gas — transforms the paste into little particles of cement and aggregate. Calera plans to desalinate the leftover water and sell it.
CaleraÂ’s cement plant is capturing 86 percent of the carbon dioxide in the flue gas from the Dynegy plant, according to a study by R.W. Beck, a consulting firm hired by Calera.
Much of the skepticism about the project stems from the acid created in CaleraÂ’s chemical process. It has to find a way to dispose of it or neutralize it by adding alkaline materials, without creating more environmental problems or raising costs. Either would be difficult to do on a large scale, Mr. Caldeira said.
Mr. Khosla said that Calera has many sources of alkaline materials and many ways to dispose of acid.
Climate scientists have raised other questions as well. “The chemical processes are known to exist, but if what you’re looking for is something that can be scaled up in order to actually mitigate CO2 emissions, it’s just a big problem,” said Ruben Juanes, assistant professor in energy studies at MIT.
Growing beyond the demonstration plant will be CaleraÂ’s next challenge, and it is a step that has stumped many clean technology start-ups.
“People have the impression that the energy sector is like the I.T. sector and you just have to build an iPhone and suddenly it will be everywhere, which is simply not the case,” said Joseph Romm, senior fellow at the Center for American Progress and editor of Climate Progress, an influential blog. “You have to build up so much infrastructure.”
Calera, which has worked with Bechtel to design and build cement plants, plans to open its first commercial plant next year. The company is in talks with Dynegy and a utility in Pennsylvania and has received grants from the Australian government to build a cement plant next to a coal plant in the state of Victoria.
“I don’t think anyone’s going to believe us until we’re up and running,” Mr. Constantz said.
Related News
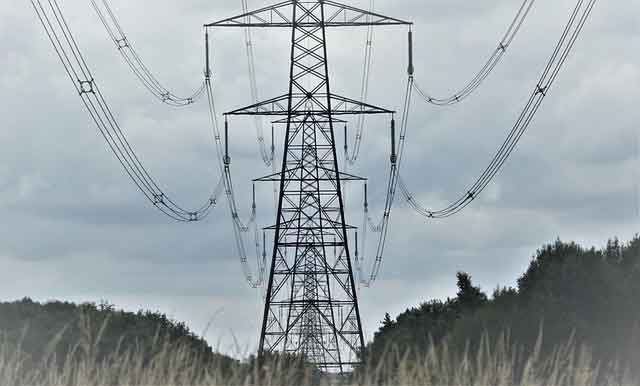
Bomb Cyclone Leaves Half a Million Without Power in Western Washington
SEATTLE - A powerful "bomb cyclone" recently hit Western Washington, causing widespread destruction across the region. The intense storm left more than half a million residents without power, with outages affecting communities from Seattle to Olympia. This weather phenomenon, marked by a rapid drop in atmospheric pressure, unleashed severe wind gusts, heavy rain, and flooding, causing significant disruption to daily life.
The bomb cyclone, which is a rapidly intensifying storm, typically features a sharp drop in barometric pressure over a short period of time. This creates extreme weather conditions, including gale-force winds, torrential rain, and coastal flooding. In Western Washington,…