Cable Cleats Testing - Crucial to Cable Management
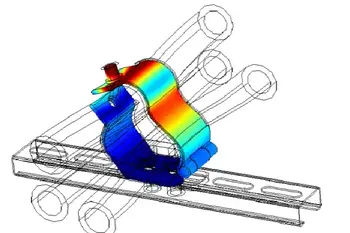
Essentially, cable cleats are devices designed to secure cables and to ensure the retention and support of them, reducing the load that the cable may be exposed to under its own weight. They are also designed to contain the cables under fault conditions, protecting the cables and the cable management system from damage.
The first European cable cleat standard, EN 50368, highlighted the retention and support that cable cleats provided to cables. Most importantly, the standard highlighted the protection of the cable management system and the potential risk to human life that could occur without the use of cable cleats.
It was not until 2003, with the release of standard EN 50368 that any formal standard for cable cleats existed. Prior to this, both cable and cable cleat manufacturers provided their own testing to their own standards for many years all over the world. This standard was then followed up with the publication of IEC 61914:2009, which further focused on the importance of cable cleat products and correct cable cleating. It set the standardised method for testing and certification of cable cleats, to prove they can withstand one or more short circuit tests. IEC 61914:2009: “6.4.3 resistant to electromechanical forces, withstanding one short circuit, 6.4.4 resistant to electromechanical forces, withstanding more than one short circuit.”
The crucial problem causing cable cleats being overlooked is that, at the moment, the implemented standards are advisory. Therefore, at times of cost cutting on cable management systems, reputable cable cleats are compromised for cheaper, lower quality versions, which aren’t certified to these standards.
Cable cleats protect the cable management system by reducing the mechanical load exerted, and ensuring the cables are fixed, retained and supported correctly.
The dangers of failing to use an appropriate cable cleat certified to IEC 61914:2009 become clear when you have seen the effects of a short circuit first hand. Without the cable cleats in place, the costs of a short circuit can be seen financially, in replacing a damaged cable management system, as well as the potential harm to individuals in the area.
Typically, damage to the cables under fault conditions occurs within the first quarter cycle of the fault. A typical circuit breaker interrupts the fault after three cycles. Whilst this may protect the equipment, the cables may have already been damaged within this short duration and may need replacing. The replacement of any cables comes at a high price as this not only includes the expensive cable costs themselves, but the labour time of decommissioning, downtime and the reinstallation of the cable management system.
Cable cleats should be designed and tested so that in the event of short circuit fault conditions, they will contain the cables without causing damage, enabling the circuit to be restored once the fault has been rectified.
The most appropriate type to use depends on the set up of the cable management system. Calculating this relies on a number of variables, such as cable construction and includes type, ratings, diameter, system design, support structure and environment.
Live trial and error testing can determine the correct cable cleat; however this method is expensive and can take weeks or months to undertake. Most installation designs are based on dated calculations, rather than live short circuit simulations because of this, which is not the most accurate cable cleat selection method. There is a wide range of options to determine the most suitable cable cleat for a given cable management system; from offering simulated solutions, to using the experience of its technical experts together with tried and tested calculations. With the cost of live testing prohibitively expensive and often impractical, one alternative option is software modelling.
On-Site Training
Interested in cost effective, professional on-site electrical training?
We can present an Electrical Training Course to your electrical engineering and maintenance staff, on your premises, tailored to your specific equipment and requirements. Click on the link below to request a Free quotation.
EF PARTNER MEDIA
Product Showcases
Shared Media