New thermal technologies come online
But a 10-kilowatt waste-heat turbine from Infinity Turbine LLC turns about a third of that waste heat into electricity.
Capturing waste heat isn't a new idea. In power generating stations, for instance, heat from turbines fired by natural gas or coal may boil water to produce steam that then drives an additional turbine to generate more power. But it has mainly been done on a large scale, using generators with capacities from 250 kilowatts up into the megawatts.
Infinity — headquartered in Madison, Wisconsin, but with assembly and testing operations in Edmonton and design and development in Delta, B.C. — focuses 10-kilowatt and 50-kilowatt units. They capture waste heat from small-scale power generation, industrial processes such as welding, and even large air-conditioning systems and use it to drive a generator, says Ulrich Schrems, the company's production manager in Delta.
And while companies like Infinity fill a gap at the lower end of the capacity scale, other researchers are finding ways to capture and make use of heat at lower temperatures than previously possible. As a result, energy that previously did nothing but overheat machine rooms is starting to provide a source of additional electricity instead.
Infinity's turbine uses a heat exchanger to transfer waste heat to a gas that then expands rapidly, exerting pressure to drive a turbine. The gas is then cooled in a condenser and goes through the cycle again.
Infinity makes the units in several sizes, Schrems says. About 15 10-kilowatt units, priced at about $15,000, have been installed to date, along with one 250-kilowatt unit at a landfill site in Brisbane, Australia, where burning methane from the landfill heats a boiler to run the turbine. Infinity also makes one-megawatt units, used mostly for testing and research.
Cyclone Power Technologies Inc. uses waste heat to drive a unique "external combustion engine" — essentially a modern steam engine. The Pompano Beach, Fla., company recently got the go-ahead from a Pennsylvania electrical utility to set up its engine at a glass products company in Hatboro, Penn., where heat from the flue of a glass furnace will generate electricity to help supply the factory.
Cyclone's system needs temperatures of 475 to 875 C, says Christopher Nelson, managing director of the company's waste heat division, and can achieve efficiency of 30 to 35 per cent. That's comparable to what mid-size turbines can do, he says, but Cyclone's system is workable on a much smaller scale - at outputs of 10 to 250 kilowatts. To put this into perspective, a typical house draws about three to five kilowatts on average, and up to about 15 kilowatts at peak times, depending on what appliances are running.
Clean Power Technologies of Newhaven, UK, has installed a trial version of its clean energy separation and recovery system, or CESAR, at a landfill site in Oxfordshire.
Methane from the landfill already powered an internal combustion engine that drives a generator and feeds about 250 kilowatts into the electricity grid. The CESAR unit extracts heat from the engine's exhaust to produce steam that drives another generator producing an additional 12 to 28 kilowatts. Mike Burns, chief technology officer for Clean Power, says his company's technology adds about 10 per cent to the system's over-all efficiency.
The CESAR technology needs 450 C to 750 C to operate, Burns says, which it can get from the exhaust of internal combustion engines and other sources. The company is also working on a plan to use heat from burning wheat husks to drive its engines.
While these technologies exploit high temperatures on a small scale, researchers at the Clean Energy Research Laboratory at the University of Ontario Institute of Technology, known as UOIT, in Oshawa, Ont., are focusing on extracting heat at relatively low temperatures.
Thirty to 40 per cent of the energy going into a steam power plant comes out as electricity. Recovering a quarter of that waste could raise overall efficiency to around 50 per cent.
One project is a chemical heat pump that captures heat at around 90 C — below the boiling point of water — and boosts its temperature to about 150 C to produce steam.
After driving a turbine in a steam power plant, steam must cool and condense before being fed back into the process, explains Ron Roberts, research associate at the lab. His heat pump needs no outside energy source because it uses some of the waste heat to drive a chemical process that returns about a quarter of the original heat at a higher temperature.
Thirty to 40 per cent of the energy going into a steam power plant comes out as electricity, Roberts says. Recovering a quarter of that waste could raise overall efficiency to around 50 per cent.
The idea has been around for a while, he says, but past prototypes have been too sensitive to small temperature variations. There is still work to do.
"I would say we're probably three to five years away from being able to take it commercial."
In a separate project, startup Marnoch Thermal Power Inc. is working with the UOIT clean energy lab to develop a heat engine that will extract power from relatively small temperature differences.
In development for four years and now being tested at UOIT, the Marnoch heat engine can work even when the temperature difference between its heat source and the outside air is as low as 10 to 30 degrees, says Ian Marnoch, the company's founder and chief technology officer.
Helped along by the Ontario Centres of Excellence and Canada Foundation for Innovation programs, Marnoch is completing a second-generation prototype now and looking for investors.
Several customers are interested and installations could begin in a year or so, Marnoch says.
Related News
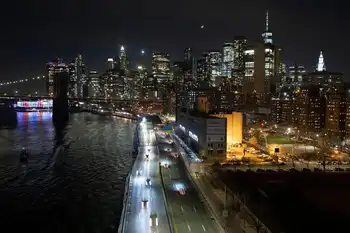
The Need for Electricity During the COVID-19 Pandemic
WASHINGTON - Dominion Energy (D) expects "incremental residential load" gains as a result of COVID-19 fallout. Southern Company CEO Tom Fanning says his company is "nowhere near" a need to review earnings guidance because of a potential recession.
Sempra Energy (SRE) has reaffirmed earnings per share guidance for 2020 and 2021, as well timing for the sale of assets in Chile and Peru. And Xcel Energy (XEL) says it still "hasn’t seen material impact on its business."
Several electric utilities have demonstrated ability to tap the bond market to lock in low-cost financing, despite ongoing turmoil. Their ranks include Dominion Energy, renewable…