Factory not too old to learn energy saving
Gerdau is one of a number of manufacturers that's benefited from the Department of Energy's Save Energy Now program, coordinated by Oak Ridge National Laboratory. The program offers private companies energy assessments and, most recently, technical assistance in projects aimed at trimming energy consumption.
The Knoxville plant was one of two facilities to make the program's list of industries that implemented more than 15 percent of DOE's energy savings recommendations.
The 240-employee factory put 40 percent of the recommendations in place, achieving 47 percent savings in natural gas usage and 18 percent in total energy savings year-over-year, said Arlan Piepho, general manager.
"Actually, the Knoxville mill is one of the more efficient mills in Gerdau and in North America," Piepho says. "We had some opportunities working with DOE, and we decided to take advantage of it."
Since the 1960s, the plant - operating continuously in its Lonsdale location since 1903 when it was owned by Knoxville Iron Co. - has recycled scrap steel to manufacture rebar used in commercial construction.
"Our raw material is scrap, and we will recycle about 1.1 billion pounds of scrap this year." Piepho says. "We're one of the largest recyclers of scrap in East Tennessee."
Melting down and processing that scrap to make the finished product requires energy - and lots of it. While declining to disclose specifics, Piepho says, "I can tell you the electric furnace in one month uses as much energy as a town of 15,000 people."
That electric furnace is the first of several energy-hungry steps in the process of melting down the scrap, converting it into semi-finished billets and re-heating and shaping the billets into finished rebar.
Gerdau invested about $500,000 in energy efficiency improvements suggested by DOE - what Piepho refers to as the "low-hanging fruit." The upgrades included replacing old equipment including a recuperator, which recycles heat and gasses in the furnace.
In one instance, buying a set of j-hooks to move 1,400 degree to 1,500 degree billets to the final rebar-making process, allowed the plant to skip a step-and save reheating costs-in which the billets were previously cooled before being transferred to another furnace to be prepped for the rolling stands that squeeze the metal into rebar.
That process change actually involved "a minimal investment," Piepho says.
While DOE's involvement was helpful in achieving the energy savings, Piepho says a culture that encourages employee feedback and a constant focus on improving operations has been key in helping the plant become more efficient - a process that really began back in 2007.
The energy initiatives have been closely tied to Gerdau's focus on safety, he says. In addition to the DOE award, the company was recognized by the Steel Manufacturers Association for zero time lost to accidents in 2010.
"You can't really have one without the other," Piepho says. "We have a very stable workforce, a very engaged workforce and, again, the safety culture, the environmental culture, the efficiency culture is something this company believes in."
Vigilance and initiative by those on the front lines of the process is important, because it's the little things that matter, he says.
"As far as energy goes, we're constantly going to look at ways to save energy," Piepho says. "We're not going to get big savings, but we know that there are still savings out there. That's how we stay competitive."
Gerdau Ameristeel is the only steel manufacturer on this year's list, but it's not the only East Tennessee manufacturer. Others are Endot Industries of Greeneville, Fujifilm Hunt Chemicals USA of Dayton and Morrill Motors of Erwin.
Related News
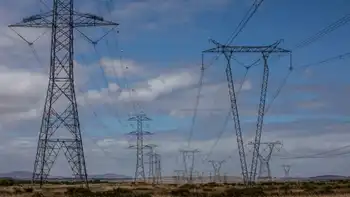
Millions at Risk of Electricity Shut-Offs Amid Summer Heat
WASHINGTON - As temperatures soar across various regions, millions of households are facing the threat of electricity shut-offs due to strain on power grids and heightened demand for cooling during summer heatwaves. This article delves into the causes behind these potential shut-offs, the impact on affected communities, and strategies to mitigate such risks in the future.
Summer Heatwave Challenges
Summer heatwaves bring not only discomfort but also significant challenges to electrical grids, particularly in densely populated urban areas where air conditioning units and cooling systems strain the capacity of infrastructure designed to meet peak demand. As temperatures rise, the demand…