Transitioning ground support vehicle fleets to electric
Airports and airlines save significantly in operating costs by implementing green transportation because it is far less expensive in the long term, according to some industry estimates. Naturally, the environmental benefit is immense, as fuel consumption is reduced and air quality is improved, especially in indoor facilities. With the growing trend toward electric equipment, the focus is now on transitioning fleets.
How do you begin to approach this transformation? How can you justify and sustain the expense? The good news is, you can ease into electrification and not get caught short when legislation begins to demand it. The even better news is, your shift to electrically powered GSE will pay for itself within a few yearsÂ… and can then start producing significant operational savings.
If you are looking to board this movement early, you will need solid support from reliable experts.
You might get some guidance from the FAAÂ’s Office of Airports Community and Environmental Needs Division or state and local based nonprofits such as the New York Power Authority, for example. It is also beneficial to cooperate with a supplier that specializes in electric vehicle systems.
It is still early in the process of electrification. There are approximately 72,000 GSE units currently in use in the United States, a mere 10 percent of which are electric; but the opportunities to go electric are everywhere. From tugs, tractors, baggage handlers, cargo loaders, belt-loaders, personnel carriers to mobile stairways, ground power units and free-standing generators, all support equipment and infrastructure will ultimately be involved in the changeover.
Conversions of combustion sources to clean electric vehicle (EV) technologies will have a major positive impact on the environment and the bottom line. As mentioned in the March 2008 edition of Ground Support Worldwide, research conducted by the New York Power Authority (NYPA) showed that a single internal combustion (IC) powered tug emits 54 tons of greenhouse gases, burning 3,248 gallons of diesel per year. And, according to John Markowitz, electric transportation engineer for NYPA, electric GSE are 90 percent cleaner and 75 percent less expensive to operate — even after taking power plant emissions into account.
Replacing existing IC-powered GSE with new EVs is best done as equipment is decommissioned. In the meantime, it is very feasible to retrofit. For example, Sacramento International Airport instituted a program to deploy 54 alternative fuel vehicles of various types. Among these vehicles were 20 belt loaders converted from gasoline to electric power, saving the airlines that owned them $10,000 per vehicle compared to purchasing new. EPRI offers a tool to assess the cost effectiveness of retrofitting from diesel to electric, based on your application. This tool can be found at http://avt.inel.gov/groundsupport.shtml.
Using the tug as an example, all the working components of an IC system can be replaced by electric. Thus, the vehicle continues to perform for its full life-span, while beginning to deliver real benefits in operational and cost efficiency, as well as the environmental benefits.
The benefits of the electric “evolution” are many. Before assessing the global impact, think about the advantages to your operation:
• Maintenance, repairs and equipment downtime are minimized, because AC motor technology is more efficient and produces less wear and tear. There is less heat and vibration generated in comparison to IC systems, and fewer moveable parts. Since electric motors do not “idle,” the hours on the hour meter are lower. They only reflect the actual work the vehicle did. Many diesel GSE spend a lot of time idling while staff load bags. In cold weather they are often left to idle for extended periods. Maintenance is based on hour meter readings.
• The ease of diagnostics is exceptional. Any maintenance issues are immediately flagged; there is no need to dismantle equipment and search manually for the source of a problem.
• The overall cost of operating an electric fleet is lower than IC. A recent study in Industrial & Utility Vehicle (IUV) Magazine of comparable industrial equipment utilized in similar circumstances to airport conditions demonstrated a break-even point of just two-and-a-quarter years. At that point, the switch to electric technology not only paid for itself, but began to generate positive cash flow versus projected fuel costs. This payback period varies depending on fuel prices, lead prices of batteries, whether rapid chargers are required, and the cost of electricity.
A study by Jeff Bowles published in IUV Sept/Oct 2008 of industrial trucks in similar operating environments to GSE, demonstrates the cost advantages of EVs. Total initial investments for EV trucks may be higher than IC, but the long-term costs for EVs are lower. Total yearly hourly operating costs per truck, per hour, were calculated to be significantly less, at $1.48 for EVs, compared to $4.93 for IC powered vehicles.
The zero emissions aspect of electrification creates measurable indoor air quality improvements. IC engines produce carbon monoxide (CO), which can accumulate in indoor areas and can cause serious health problems, including death. While it is too early to quantify the savings in productivity and paid employee sick days, it is safe to assume this is another area of significant cost reduction with important human resources ramifications.
Operators will experience these advantages while achieving equal or better performance from their electric equipment. Of course, there is the consideration of the reduction of fossil fuel consumption for global environmental benefits.
Careful planning is needed to meet the very different requirements of an electric fleet. The airport facilities need to plan for new infrastructure requirements, such as power lines for charging stations, traffic routing to and from chargers, etc. Maintenance cycles and charging methodologies must be considered when planning for the electric fleet.
To avoid equipment downtime, “opportunity-charging” methods coupled with “fast-charge technology” is the solution. While a standard charge profile is 8-12 hours, fast chargers can put back 80 percent of charge in two hours or less. In fact, this rapid-charge profile is a requirement of the FAA’s Electric Aircraft Push-Back Tractor Tech specification. Rapid-charge power stations need to be logistically placed so equipment operators can conveniently plug in whenever the vehicle is not in use.
To determine the best strategic locations, GSE planners need to consider:
• Airport configuration and regulations
• Traffic patterns to and from stations
• Sufficient power supply (In airports without sufficient power a technology called bridge power sharing is used. The jetway used to board passengers has a large electric motor that is only used about two minutes per hour. That electrical circuit can support rapid battery chargers when the jetway motor is not being used. This technology also reduces installation cost significantly since wire and conduit runs are shorter.)
• Appropriate operational room
In the meantime, careful planning and training will optimize both vehicle and driver productivity. The payback is significant. In addition, the cleaner-running GSE operation can collect Air Quality Credits from the airport authorities.
Service fleet operators will need training on:
• Differences in driving and operating
• Maintenance, trouble-shooting and diagnostics
• Charging methods and habits
• Instruments, controls, etc.
• Air Quality Credits
• New mindset: embracing change
No getting around it — electrification encompasses major initiatives, such as the removal of gas tanks. Government support is available and more incentives can be anticipated.
Current FAA initiatives include:
• VALE (Voluntary Airport Low-Emission) Program, begun 2005, is focused on lowering ground emissions at commercial service airports in designated air quality non-attainment areas.
• ARB (California Air Resources Board) programs include Public Interest Energy Research (PIER), which supports R&D via contracts and grants for energy technology and related scientific activities.
While we are still in the infancy of this initiative, there has been nearly a decade of progress in North America. One of the first markers of the evolution was an electric ground support equipment roundtable held in 2000 by the Electric Power Research Institute in Sacramento, California. In fact, the state of California continues to be a major force in the changeover. As of 2009, it is requiring forklift fleet owners to maintain specified average emission levels per truck. It is logical to expect other states to follow suit.
The switchover to electric GSE is clearly underway and here to stay. Many voluntary incentives are available from state governments and the FAA. Starting the switch to electric technology for GSE demonstrates the airportÂ’s commitment to a cleaner environment. ItÂ’s good public relations and good business, too.
Curtis Instruments is a manufacturer of motor control, instrumentation and power conversion products for electric vehicles. The company was established in 1960 and serves the worldwide vehicle OEM market.
Southwest Airlines: in the past seven years, saved millions of dollars in a 14 million gallon fuel reduction achieved by switching gate procedures to electric power.
Continental Airlines: met the 2007 Emission Reduction goal of the Texas Commission on Environmental Quality in 2005, gaining Air Quality Credits and enhancing their brand image in the very competitive consumer marketplace.
American Airlines: an EPRI-organized pilot project at Detroit Metro Airport electrified 132 GSE in 2000 and is on the way to completing the entire fleet changeover of nearly 1,100 vehicles.
Related News
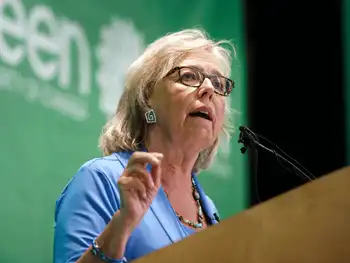
Elizabeth May wants a fully renewable electricity grid by 2030. Is that possible?
TORONTO - Green Party Leader Elizabeth May has a vision for Canada in 2030. In 11 years, all new cars will be electric. A national ban will prohibit anyone from buying a gas-powered vehicle. No matter where you live, charging stations will make driving long distances easy and affordable. Alberta’s oil industry will be on the way out, replaced by jobs in sectors such as urban farming, renewable energy and retrofitting buildings for energy efficiency. The electric grid will be powered by 100 per cent renewable energy.
It’s all part of the Greens’ “Mission Possible” – a detailed plan released Monday…