Construction sector slow to embrace hybrids
Hybrid excavators, bulldozers and wheel loaders have been operating in other countries for several years.
In Canada, except for electric haul trucks, hybrid equipment, most often electric-diesel systems, have typically been in the test stages.
In May, KomatsuÂ’s Hybrid PC200LC-8 excavator was demonstrated in Surrey, later moving east across Canada.
Another one underwent extensive testing in Montreal, with users supplying feedback to Komatsu. But for now, there are no plans to sell the machine in North America, said Mari Aoyagi, KomatsuÂ’s public relations and communications manager for North America.
KomatsuÂ’s intention was to find out how users responded to the excavator and whether they were willing to pay roughly 50 per cent more for the piece of equipment over the conventional PC200LC-8, which costs about $200,000.
Where the difference comes in is that the hybrid generates up to 40 per cent in fuel savings, Aoyagi said from Chicago.
“We want to find out how the marketplace would feel about the price premium,” she said.
Already, feedback is leading Komatsu to consider design changes to the excavator, so that it can be mass-produced at a lower cost. There have also been comments about the hybridÂ’s muted operation.
North American operators prefer loud machines, which they equate with power. The louder a piece of heavy equipment is, the more powerful they deem it to be.
“The challenge is getting them to accept a quieter machine,” Aoyagi said.
“Because it’s so quiet, they become suspicious that it isn’t doing its job.” But the hybrid can do everything the standard PC200LC-8 can, and with less racket.
ItÂ’s unfortunate workers expect a high volume of noise because using a quieter machine is not only safer for the operator, itÂ’s also easier on their body, particularly their hearing, Aoyagi said.
“We’ve been trying to coach the operators,” she said. To achieve the quieter operation, the hybrid excavator uses an electric swing motor, power generator motor, capacitor and diesel engine.
The unique design works on the principle of swing energy, regeneration and energy storage, achieved with the machineÂ’s ultra-capacitor.
Kinetic energy generated during the swing braking phase is converted to electricity sent through an inverter and captured by the ultra-capacitor.
Captured energy is discharged for upper structure rotation and to assist the engine as commanded by the hybrid controller, explained Tony Kosolofski, Western Canada district manager for Komatsu Canada.
Because the swing is based on an electric drive, itÂ’s faster, which in effect increases productivity, Aoyagi said.
And with energy accessed from the ultra-capacitor rather than the battery, itÂ’s not affected by temperature changes.
Another advantage is that the hybrid doesnÂ’t run at high RPMs all the time, especially if itÂ’s doing lighter work.
“But what really grabs your attention are the fuel savings which result in lower operating costs,” Kosolofski said. Lower emissions are another bonus, he added.
In 2009, Komatsu introduced 700 of the Hybrid PC200LC-8s with 500 operating in China and another 200 in Japan, which has some of the highest fuel costs in the world, roughly 75 per cent more than in Canada.
The energy-efficient excavators have been big successes in both countries, where quieter machinery is preferred, Aoyagi said.
In September, Volvo Construction Equipment has scheduled the release of its L220F Hybrid wheel loader, the prototype first unveiled in North America at the 2008 Conexpo show in Las Vegas, said Scott Cairns, Vancouver Island manager for Great West Equipment.
The electric-diesel hybrid uses an integrated starter generator ISG that is fitted between the engine and transmission.
The ISG is coupled to a super battery that has many times the power of a regular lead acid battery.
Fuel is saved because the ISG provides power only when the operator needs it. Fuel reductions can be up to 25 per cent, Cairns said from Nanaimo. Up to 40 percent of a wheel loaderÂ’s time can be when the engine is idling.
The ISG allows the diesel engine to be turned off when not moving and then started almost instantly.
Other benefits include a faster takeoff at lower revs and an electric motor that generates high torque.
Cairns said customers are doing everything they can to save operating costs and one of the easiest ways to save is via fuel consumption.
While he didnÂ’t have a sticker price, heÂ’s expecting the Volvo hybrid wheel loader to be a big seller.
And, a hybrid heavy equipment discussion wouldnÂ’t be complete without an entry from Caterpillar.
The Illinois-based company has built the worldÂ’s first diesel-electric bulldozer, the D7E. Costing roughly $700,000 new, Caterpillar said the dozer achieves a 25 percent increase in fuel efficiency, in effect paying for itself after three years.
The D7EÂ’s diesel-electric drive train includes a generator, electric motors and power electronics.
The electrical drive components, while technically advanced, are mechanically simpler.
There are no friction clutches and fewer moving parts overall. The D7E doesnÂ’t have a driveshaft nor does it use engine belts.
Related News
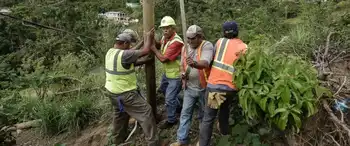
Electricity restored to 75 percent of customers in Puerto Rico
PUERTO RICO - Nearly six months after Hurricane Maria decimated Puerto Rico, the island's electricity has been restored to 75 percent capacity, according to its utility company.
The Puerto Rico Electric Power Authority said Sunday that 75.35 percent of customers now have electricity. It added that 90.8 percent of the electrical grid, already anemic even before the Sept. 20 storm barrelled through the island, is generating power again.
Thousands of power restoration personnel made up of the Puerto Rico Electric Power Authority (PREPA), the Federal Emergency Management Agency (FEMA), industry workers from the mainland, and the Army Corps of Engineers have made…