Billions wasted when replacing failed motors
This is because organizations across the board continue to specify motors based on lowest capital cost, rather than looking at total cost of ownership.
“If you look at the total cost of operating an electric motor over its typical 20 year service lifetime, you will find that the initial purchase price of the motor represents about 2% of the total lifetime cost,” said Valone Gomes, national OEM sales and product manager at WEG Electric Motors Corp., “whereas 97% of the total expenditures are for the electricity to power the motor. Clearly this means that motor efficiency and reliability should be the principle selection criterion, not the cheapest initial purchase price.”
Gomes explained that since the passage of the Energy Policy Act of 1992 (EPAct), U.S. industry had to meet certain minimum electrical efficiency standards when replacing electric motors. These were embodied by a class of EPAct high efficiency motors which represented a snapshot of the best available motor technology available around 1990 to gain 1 to 4% in efficiency.
But, technology has improved considerably, and a new class of motors — called NEMA Premium Efficiency (NPE) motors — is now available from suppliers throughout the industry. NPE motors deliver efficiencies of 1 to 4% above EPAct designs, but are more expensive to manufacture and so have initial cost premiums of 10 to 30% over EPAct units.
“So the vast majority of people replacing a motor will buy the EPAct variety based on its lower initial purchase cost,” Gomes said. “But by selecting an NPE motor for the same application, they could have saved the purchase premium in as little as two or three months in reduced electricity bills, and pay for the entire motor in less than 3 years based on the lower energy costs during that period. And this does not take into account the programs sponsored by local governments and utilities that subsidize the purchase of higher efficiency motors with rebates, tax credits, and other incentives.”
Gomes noted that, “NEMA Premium Efficiency motors will be required for motor replacement after 2010, when the Energy Independence and Security Act comes into force. But in the meantime, U.S. industry could be saving million of dollars a years if they selected motors based on lifetime cost rather than purchase price.
“In fact, the Department of Energy has estimated that switching exclusively to NEMA premium motors would save U.S. industry more than $10 billion annually, and reduce carbon emissions by nearly 80 million metric tons – the carbon equivalent of taking 16 million autos off the road. That’s good business and good environmental citizenship.
Related News
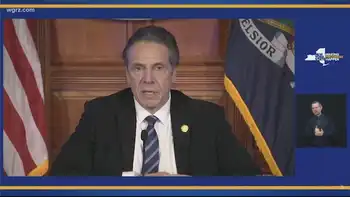
New York State Moratorium on Utility Disconnections During Emergencies
NEW YORK - Governor Andrew M. Cuomo has announced a proposal to prohibit utility disconnections in regions that are under a state of emergency as part of the 2021 State of the State. The Governor will propose legislation that will apply to electric, gas, water, telecommunications, cable and internet services. Utilities that fail to comply will be subject to penalties.
“In a year in which we dealt with an unprecedented pandemic, ferocious storms added insult to injury by knocking out power for hundreds of thousands of New Yorkers,” Governor Cuomo said. “Utility companies provide essential services, and we need to make…